At our last club meeting one of our members displayed on the show-n-tell table a coffee scoop which was composed of two turned parts - bowl and handle - which had been fastened together to create the final piece. I decided to turn a coffee scoop out of a single piece of wood, and picked zebrawood to maximaize the effect of the striking grain. This process requires first turning the handle and the bowl end as a sort of "lollipop" shape (see first photo, on table top). Then you remount the piece "sideways" (in a jam chuck turned for the purpose), so that as the piece turns the handle is flying around and round in the same plane as the scoop-to-be. Then you hollow out the scoop part just as if it were a tiny bowl. The finished scoop measures 5" in total length, and the bowl is 1 1/2" in diameter. It holds approximately one tablespoon. You can find instructions online for turning either the one-piece or the two-piece scoops.
On this blog I post photos and commentary regarding my woodturning (and, occasionally, woodworking) projects. While my efforts to stay current by adding new photos and descriptions sometimes fall behind, keep checking back to see what's new. Comments are appreciated.

Sunday, December 19, 2010
Tuesday, November 23, 2010
Bernie's Birthday Bowl
I turned this large cherry salad bowl as a birthday present for my wife. It measures 13" across the rim and is 5 1/2" deep. (Holds quite a lot of salad!) The bowl definitely looks taller than 5 1/2" - I believe that is the effect of the sweeping curve from the rim to the relatively small base.
Monday, November 22, 2010
More laminated off-center pendants, but no pics
For reference, see the April 25, 2010 post. The laminated off-center pendants proved to be a best-seller at the Olbrich Gardens show. Unfortunately (?) they all sold out, and I didn't get any close-up pics of the display - you can see some of them in one of the table photos in the Olbrich post, below. I only had a chance to turn one pendant out of the brightly colored, laminated gun-stock material (see the bottle stoppers), which also sold. So I'll have to do some more, I guess....
Bottle stoppers revisited - 2010
I turned a number of new bottle stoppers for the Olbrich Gardens show, some of which were pretty colorful. These were turned from laminated, dyed beech gunstock material provided by a member of our club (and which I won at a club raffle).
Olbrich Gardens Show
For the past several years, in late October, Badger Woodturners, my turning club, has gotten together with the Madison Area Woodcarvers for a show and sale at the Olbrich Botanical Gardens. On the woodturning side about ten of us had sales tables, and the club also ran two demo lathes throughout the day, and also had a raffle of a large number of turnings donated by members. This year's show was very successful, and most of us who had items for sale did reasonably well. Smaller items tended to sell better than larger, more costly ones, reflecting the overall state of the economy.
In the "Links" column to the left I've added a link to the Badger Woodturners' recently created website, where you can read our newsletters (which also include photos of members' work) and find out a little more about the group.
Harbor Athletic Club, where my wife and I work out, permits members to post advertising displays in a couple of windows in the club lobby. I used the opportunity this year to advertise the Olbrich show and my participation. The display drew a number of nice comments.




In the "Links" column to the left I've added a link to the Badger Woodturners' recently created website, where you can read our newsletters (which also include photos of members' work) and find out a little more about the group.
Harbor Athletic Club, where my wife and I work out, permits members to post advertising displays in a couple of windows in the club lobby. I used the opportunity this year to advertise the Olbrich show and my participation. The display drew a number of nice comments.





Natural edged cherry crotch bowl
This a natural edged cherry crotch bowl which I turned earlier this year. "Natural edged" means that the bowl was turned with the center of the trunk forming the bottom or base of the bowl, and the bark on the outside of the trunk forming the top or rim. (This is the reverse of the orientation in which traditional bowls are turned.) A "crotch" is the intersection where the trunk splits into two or more sections, or a limb branches off from the trunk. You can often get some very interesting figure there. This bowl measures about 9" across by 4" deep. I sold it at the October 2010 Olbrich Gardens show (see next entry).











Thursday, September 09, 2010
Unusual Pens
We had a pen making challenge for our September meeting, and I turned a couple of somewhat unusual pens for it. While most wood-turned pens incorporate hardware kits, with all of the metal pieces provided, I'd seen a demo some years back involving the turning of a 100% wood pen that incorporated the innards of a simple Bic stick pen. Here's the process: you drill an appropriately sized hole in the end of your blank, turn your pen, pull the innards out of the Bic, and insert them into your pen. Voila! Pretty simple, and allows for lots of variations. [If you're interested in the turning details, drop me a note.] I did two pens, of slightly different styles, both pretty long (8 1/2" and 9 1/4"). I've discovered that long pens are less likely to disappear on the desk or be mislaid. The longer of these two pens incorporates a "captive ring" (see last photo), which I turned using old dental scrapers I'd acquired from Sue, the very kind hygienist who cleans my teeth (and to whom I have since given the pen)! (Basically a captive ring is just a ring of wood turned loose, in place, from the same piece that holds it; they're a little tricky to do, at least with a tight fit.)











Sunday, August 29, 2010
I didn't turn this, but I wish I had - Japanese Winged Box
Last week end I attended the Chicago Area Woodturners' three-day symposium, "Turn On! Chicago." As in 2008, it was held at the St. Mary's on the Lake Seminary campus, in Mundelein, IL - an incredibly beautiful campus setting. About 220 of us were there for a series of ten rounds of demonstrations by professional and very talented amateur turners. There were five alternative venues for each round, so there was a great deal of picking and choosing. Among the sessions I attended were three by Jimmy Clewes (originally from New Castle, England, and now Las Vegas, NV) and three with Cindy Drozda (of Boulder, CO).
At the charity auction following our Saturday night dinner, I had the good fortune to bid in the demo piece that Jimmy had turned at one of the sessions I had attended - the Japanese Winged Box shown in the photos below. He turned the base from a solid piece of cherry 10" x 4" x 2" mounted on a screw chuck and running at an incredibly fast 3200 rpm. It sounded like a close-up airplane propeller! For purposes of the demo he also made the box lid (turned from a separate block of cherry) snap-on tight, so you have to pry it off. (You wouldn't do this for a gallery piece, but this was a show-off piece for turners.) And he did all this in less than an hour and a half while talking about what he was doing and telling stories at the same time. really amazing!
I've added a link to Jimmy's web site in the links column to the left.




At the charity auction following our Saturday night dinner, I had the good fortune to bid in the demo piece that Jimmy had turned at one of the sessions I had attended - the Japanese Winged Box shown in the photos below. He turned the base from a solid piece of cherry 10" x 4" x 2" mounted on a screw chuck and running at an incredibly fast 3200 rpm. It sounded like a close-up airplane propeller! For purposes of the demo he also made the box lid (turned from a separate block of cherry) snap-on tight, so you have to pry it off. (You wouldn't do this for a gallery piece, but this was a show-off piece for turners.) And he did all this in less than an hour and a half while talking about what he was doing and telling stories at the same time. really amazing!
I've added a link to Jimmy's web site in the links column to the left.





Sunday, July 04, 2010
Cherry burl finial box
A professional turner named Cindy Drozda specializes in turning very small boxes with very delicate finials; they are exquisite. (I've added a link to her website in the "Links" list in the left margin.) My friend John Nicholson has studied the techniques she teaches, and has turned many similar boxes himself. A couple weeks ago he gave a step-by-step demonstration of this process for a small wood turners' group, and I went over to his shop to handle the video camera for him. After watching the demo I was inspired to try one myself, and these photos reflect the result. My box is not as small or delicate as the professionals', but I think it came out pretty well. The main wood is cherry burl; the rim and foot are bloodwood. This box is 2 1/8" in diameter at its widest point, and 4 5/8" tall.

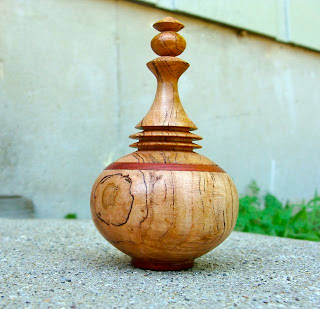



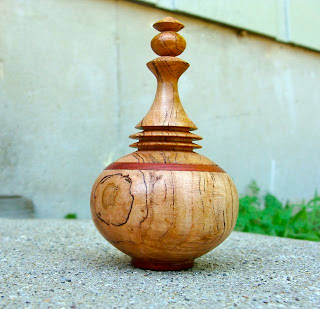



Tuesday, May 11, 2010
Ellsworth-style birch closed form

In April David Ellsworth, one of the best and best-known professional turners in the US spent a three-day week end with our group, talking, demonstrating, teaching and critiquing. On Friday night Brent English had a reception at his Robust Lathe shop, where David showed slides and discussed his work. On Saturday, at Dave Hiller's shop, about 50 of us watched David do all-day demos of his techniques, during which time he turned a standard bowl, a natural edged bowl, and a closed-form vessel. (In the photo he's working on the last of these.) Then on Sunday he held a hands-on class for 8 turners. I attended the Friday and Saturday sessions, but could not attend Sunday's. I did, however, attempt to emulate David's technique in turning a closed-end form, and the photos below reflect my result. The piece is turned from an old birch log, and is unfinished and mostly unsanded. It is about 4" in all dimensions and fully hollowed. I've generally described the process by which this is done following the photos. I've also added a link to his studio website in the Links I Like section in the left-hand column.





Here's more than you want to know about how this is done. David's approach to turning such a piece (and the technique which I used here), is to mount the log blank lengthwise between centers on the lathe, and turn it into a cylinder of roughly the diameter of the piece you want to turn. You then turn the piece as fully round (ball-shaped) as possible, leaving only tenons on each end where the piece is held on the lathe. Then you take the piece off the lathe, turn it 90 degrees, and mount it between centers again, this time on the surface of the round ball. Then you turn off the remains of the original tenons (achieving a nearly round shape) and turn a new tenon at one end, shaped be held in a chuck. Finally, you again remnove the piece from the lathe, and remount it with the new tenon held in your chuck. Then you hollow it out! (Why do all of this? You don't have to if you want an end-grain vessel - i.e., one where the grain runs vertically from the base to the opening in the top. But the technique shown and described is used if you want the grain to run across the piece instead of up and down. Also, it's the best way to get a really round shape.)
Subscribe to:
Posts (Atom)